
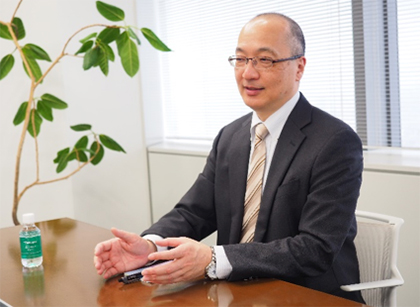
Aiming to improve the overall quality of our products, supply, and services, Terumo has built a supply chain capable of reliably and swiftly supplying high-quality products to over 160 countries and regions across the world. Even as COVID-19 continues to spread globally, this fundamental approach has not changed. We have ensured a continuous supply of products throughout the pandemic (as of April 30, 2021).
Production at Terumo is handled by 32 factories around the world. In fiscal 2019, we established a new function: the Chief Manufacturing Officer (CMO). The CMO’s role is to oversee the entire supply chain—from material procurement to production and supply—and to manage and leverage our "monozukuri" (manufacturing) capabilities across the Group. In the case of the COVID-19 pandemic, where the situation changes every minute, being able to share the latest information with each production site in a timely manner affects our ability to supply products later on. This global operation structure has come to play a vital role in this regard.
Spreading knowledge across the Group to protect production
I received the first report of an infectious disease outbreak caused by an unknown virus back in January 2020. This information came to me through a report by an associate (employee) at our factory in Hangzhou, China. From my experiences with past pandemics, as well as the timing of the Chinese New Year coming up in February and a large number of people in the Asian region would be on the move, I sensed that this infectious disease could spread worldwide. Some of Terumo’s production sites have thousands of associates working in there. If an outbreak were to occur in one of these sites, we might be forced to suspend operations. Therefore, I contacted all factories and related departments at once and began to consider infection prevention measures and estimate the extent of impact.
The first thing I did was to conduct internal interviews to figure out what our initial response should be. In fact, the Hangzhou Factory was knowledgeable about dealing with infectious diseases due to past experiences, including the Severe Acute Respiratory Syndrome (SARS) outbreak. I asked them: What kind of arrangements should be made? What kind of situations could we expect in the future? What did we need to do to prepare for those situations? Were there currently any problems? The answers they provided were promptly shared with other production sites. It was at that time that we also obtained the information that the cafeteria was one of the places in the factory where the risk of infection was highest. Having learned this, around February 2020—before the disease fully took off globally—I recall that some of our factories in Japan had already begun installing acrylic panels to prevent respiratory fluid transmission in their cafeterias and introducing staggered mealtimes.
-
Acrylic panels were introduced to cafeterias at production sites in Japan
From the outset, Terumo has been strongly aware of the need to keep work environments and products clean due to the nature of our business, in which we handle medical products. This has worked in our favor during the COVID-19 pandemic, as we were able to add more infection prevention measures on top of regular efforts to maintain a clean environment without much difficulty. These measures were adopted uniformly across the countries and regions in which we operate, and I feel that everyone handled it smoothly.
Ensuring an unbroken chain from material procurement to production and supply
Our existing business continuity plan (BCP) for the supply chain had been primarily designed to address natural disasters. In other words, it focused on measures in case of localized damage to infrastructure such as electricity, the water supply, and our production facilities, and it assumed to require a relatively short period of time for restoration. However, the scale of this pandemic is beyond anything we have seen in recent years, with the virus spreading simultaneously throughout the world. Its effects are so prolonged that there is no end in sight. Although our production facilities were not damaged, we faced many situations that were not in the scenario, such as the possibility of production being stalled because associates could not come to work due to lockdowns. In each case, we approached to local governments and authorities to obtain their understanding and support in order to continue production, while making every effort ourselves.
In terms of parts procurement and logistics, we went through an extremely challenging time when suppliers stopped or reduced production, many flights were cancelled, and shipping rates were raised. Despite all of this, I believe that there are two factors behind why Terumo has been able to keep delivering products without falling significantly behind the demands of the market. One is, again, information sharing. We created a space for the people in charge at each production site to gather on a weekly basis and communicate across function lines, that is, across the procurement, production, and supply chain functions. By pooling our knowledge and supporting each other, we are striving to secure new suppliers and alternative routes. The other is the fact that we had stockpiled the right amount of inventory in each region during pre-pandemic times. Our ability to effectively utilize these stockpiles has also greatly contributed to maintaining our supply system.
Making decisions without hesitation in order to support healthcare
The current pandemic has once again brought our attention to the need to build a supply system that considers the global and long-term effects of a disaster. Going forward, we will redefine our BCP and further enhance measures such as increasing supply chain visibility, strategically stockpiling inventory, securing multiple purchase routes, and dividing our production sites into multiple locations.
Terumo manufactures products. However, these are not products that everyone can wait for until they are supplied. This is because some of these products are directly tied to patients’ lives. When I look back on the past year and a half, I think that the biggest factor that allowed us to keep delivering products to medical settings without a significant disruption to our steady supply, even throughout the COVID-19 pandemic, was that each and every one of us had no hesitation in our actions. All of us have the feeling that there is a medical treatment that could stop if we do not continue to supply our products, and that we have a responsibility to fulfill for the sake of patients and healthcare professionals around the world. Regardless of the country or region, our associates embrace these same principles and are committed to upholding them. Since everyone is working toward the same goal on a daily basis, each one of us can make the best decision quickly on our own without waiting for instructions, even if an unexpected crisis occurs. The same culture of mutual support is being cultivated at Terumo irrespective of national or other boundaries—this is very encouraging.
Terumo has been, and will continue to be, committed to providing a steady supply of products utilizing the Group’s global network in charge of the supply chain. Our entire Group will work together to ensure that we can continue delivering high-quality products to patients awaiting treatment and to healthcare professionals who are battling COVID-19 in medical settings where they face the risk of infection.